Advanced Features
In this section, a more detailed look will be taken at some of the operational aspects of the new features introduced with MOST. Specifically, we will focus on the pre-processing part in which all the data necessary for simulating Floating Offshore Wind Turbines (FOWT) and hybrid platforms are obtained. For the simulation and post-processing part, please refer to the theory section of MOST (Theory) and the advanced features of WEC-Sim (Advanced Features).
MOST-IO
The pre-processing phase of MOST takes place through the use of the mostIO.m
script in the ‘’mostData’’ subfolder, through which the following scripts
are launched (in this order):
run_turbsim.m
: creation of the data structure describing the input wind speeds;Create_Mooring_Matrix.m
: creation of the look-up table describing the mooring forces;BladeData.m
: creation of the data structure concerning the characteristics of the airfoils constituting the turbine blades;WTproperties.m
: creation of the data structure concerningo the geometric and inertial characteristics of the wind turbine;Steady_States.m
: computation of the steady-state values of certain quantities of interest when the average wind speed varies and used for the calculation of some quantities concerning the control logic;Controller.m
: creation of the data used to simulate the control logics (Baseline [D3] or ROSCO [D4])AeroLoads.m
: creation of the aerodynamic loads look-up table (acting on the blades root).
In the next subsections, MOST features will be discussed in detail, in particular, the settings to be provided to obtain the required data and the operations performed in the various codes will be explained.
Wind Features
Wind speed can be defined by choosing between the two options of the wind class:
Constant wind conditions
Turbulent wind conditions
The constant wind speed is constant in time and space while the second option includes the temporal and spatial turbulence of the wind. Below is an image of the Variant Subsystem through which one of the two wind options can be enabled.
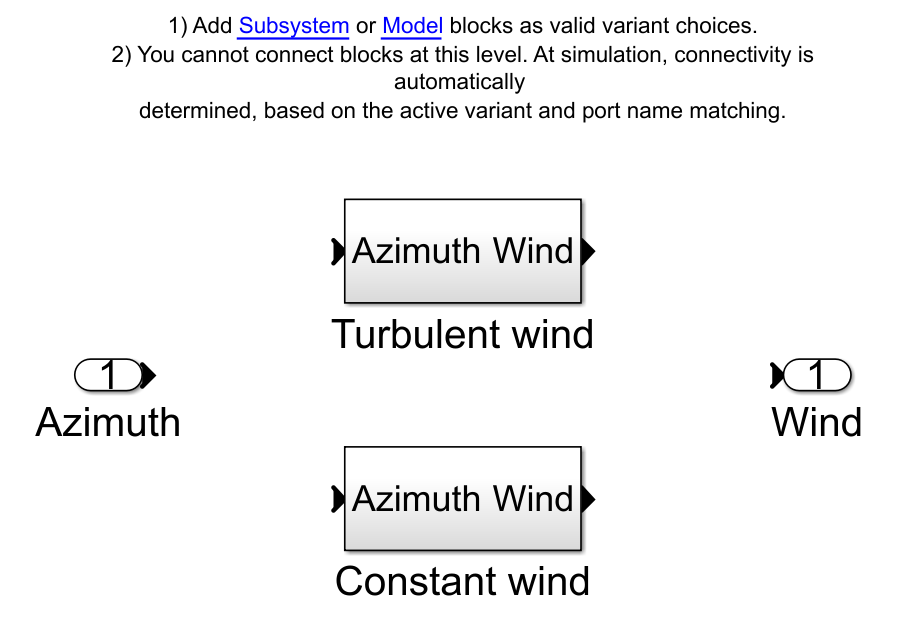
The simulation of the wind turbine for turbulent wind conditions requires the generation of a look-up table which relates the temporal and spatial
variation of wind speed on the wind turbine rotor plane (yz plane). Therefore the wind speed is discretized for 3 variables (2 spatial parameters,
y and z, and the time). The look-up table is generated using run_turbsim.m
which computes turbulent wind field based on Turbsim
executable. Mean wind speed can be defined in run_turbsim.m
script, while other parameters can be set-up in the Turbsim_inputfile.txt
file,
the main ones are:
Name |
Description |
|
Vertical grid-point matrix dimension |
|
Horizontal grid-point matrix dimension |
|
Time step [s] |
|
Length of analysis time series [s] |
|
Usable length of output time series [s] |
|
Hub height [m] |
|
Grid height [m] |
|
Grid width [m] |
|
Vertical mean flow (uptilt) angle [deg] |
|
Horizontal mean flow (skew) angle [deg] |
|
Turbulence model (“IECKAI”=Kaimal, “IECVKM”=von Karman, “GP_LLJ”, “NWTCUP”, “SMOOTH”, “WF_UPW”, “WF_07D”, “WF_14D”, “TIDAL”) |
|
Number of IEC 61400-x standard (x=1,2, or 3 with optional 61400-1 edition number) |
|
IEC turbulence characteristic (“A”, “B”, “C” or the turbulence intensity in percent) |
|
IEC turbulence type (“NTM”=normal, “xETM”=extreme turbulence, “xEWM1”=extreme 1-year wind, “xEWM50”=extreme 50-year wind, where x=wind turbine class 1, 2, or 3) |
|
IEC Extreme Turbulence Model “c” parameter [m/s] |
|
Wind profile type (“JET”;”LOG”=logarithmic;”PL”=power law;”H2L”=Log law for TIDAL spectral model;”IEC”=PL on rotor disk, LOG elsewhere) |
|
Height of the reference wind speed [m] |
|
Power law exponent [-] |
|
Surface roughness length [m] |
|
Hub mean u’w’ Reynolds stress |
|
Hub mean u’v’ Reynolds stress |
|
Hub mean v’w’ Reynolds stress |
A detailed description of using Turbsim is given here [D2].
Aerodynamic wind loads calculation in the Simulink model requires the average wind speed for each blade. This is found by computing the average wind speed for four discretized points along the blade length during the simulation. Relative wind speed for each blade is computed including the influence of the horizontal hub speed and the pitch and yaw rotation of the hub.
Mooring Features
MOST allows for simulation of a mooring look-up table to model a quasi-static, non-linear mooring system. Specifically, the mooring look-up table simulates a mooring system consisting of a certain number of lines suspended between two points (anchor and fairlead) and angularly equispaced. This option is based on the catenary equations similarly to the open-source code MAP++ [D1].
In the simulink model, forces and torques due to moorings are determined through 6 different look-up tables having the 6 degrees of freedom surge,
sway, heave, roll, pitch, and yaw as inputs. The breakpoints (related to the inputs) and the outpus (Fx, Fy, Fz, Mx, My and Mz, i.e., the mooring
loads) are contained within a data structure called “moor_matrix” and created through the Create_Mooring_Matrix.m
script, in which the following
variables are specified:
Water density (kg/m^3):
rho_water
Gravity acceleration (m/s^2):
gravity
Water depth (m):
depth
Mooring line diameter (m):
d
Linear mass (kg/m):
linear_mass
Number of lines:
number_lines
Fairlead and anchor positions of the first line (m):
nodes
Mooring lines unstretched length (m):
L
Sectional stiffness (N):
EA
Seabed friction coefficient:
CB
In addition, the user can specify the domain of the look-up tables, specifically:
Amplitude and discretisation along surge direction (m):
X
Amplitude and discretisation along sway direction (m):
Y
Amplitude and discretisation along heave direction (m):
Z
Amplitude and discretisation around roll axis (rad):
RX
Amplitude and discretisation around pitch axis (rad):
RY
Amplitude and discretisation around yaw axis (rad):
RZ
The code for generating the “moor_matrix” structure at first calculates the positions of the fairleads and anchors of the other lines, in accordance with the specified number and in an angularly equispaced manner, after which, for each combination of the inputs (surge, sway, heave, roll, pitch, and yaw) it calculates the new positions of the fairleads. Given these positions, for each line it performs a numerical optimization by which the vertical force and the horizontal force (along the projection of the line in the xy plane) are calculated. Specifically, by means of the typical catenary equations, it is possible to calculate (knowing the characteristics of a line) the above-mentioned vertical and horizontal forces having as input the vertical and horizontal distances between the two ends of the line, so, in this case the optimization procedure searches for forces such that the distances are as close as possible to those specified. Once the vertical and horizontal forces are calculated for each line, the resulting force and torque in the global reference frame are applied to the origin of the reference frame attached to the structure.
Wind Turbine Features
The wind turbine is modelled as a multi-body system including the tower, the nacelle, the hub, and the blades. The properties of each wind turbine component
are defined in two structures that can be generated using the provided BladeData.m
and WTproperties.m
MATLAB codes. In the first, the
variables concerning the blades are defined, specifically (see figure below for a better comprehension):
Blade radius values for which other properties are defined:
radius
Value, for each specified radius, of the pre-bending distance out of the rotor plane:
BlCrvAC
Value, for each specified radius, of the pre-bending angle out of the rotor plane:
BlCrvAng
Value, for each specified radius, of the pre-bending distance in the rotor plane:
BlSwpAC
Value, for each specified radius, of the twist angle:
twist
Value, for each specified radius, of the chord:
chord
Index of the airfoil type corresponding to each specified radius:
airfoil_index
Matrix containing, for each type of airfoil existing, the values of lift, drag and torque coefficients as a function of angle of attack:
airfoil
The following figure [D9] shows some of the values mentioned above.
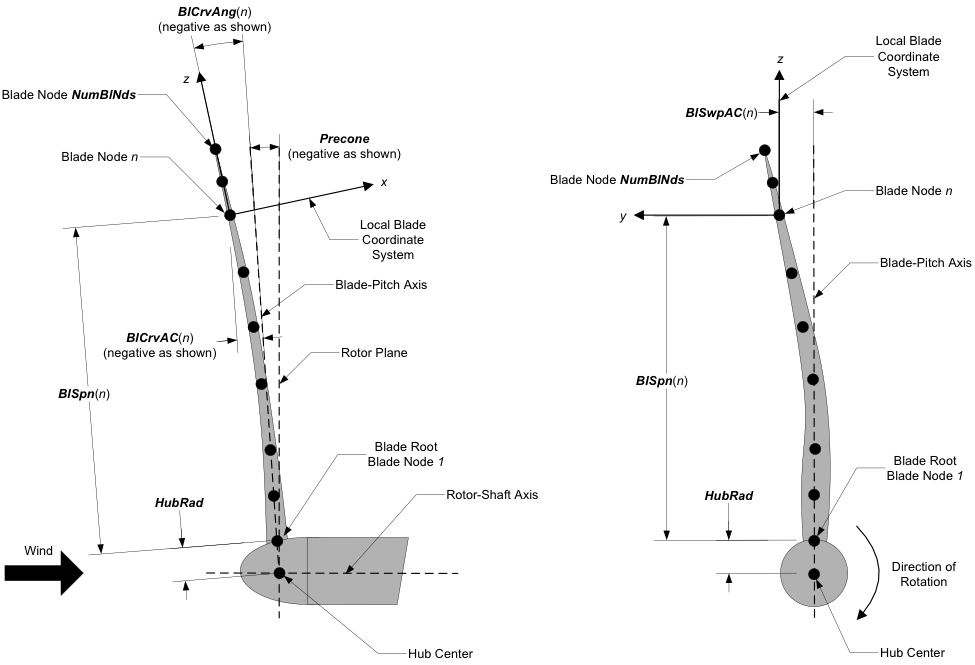
In the second script, the geometric and inertial properties of the turbine components are defined. For each of them the mass and inertia are defined, in addition, the following other variables must be entered (see figure below for a better comprehension):
Tower offset position relative to sea water level (m):
tower.offset
Tower height (m):
tower.height
Tower relative center of mass (relative to tower offset) (m):
tower.cog_rel
Nacelle relative center of mass (relative to tower top) (m):
nacelle.cog_rel
Twr2Shft (deg):
nacelle.Twr2Shft
Tilt angle (deg):
nacelle.tiltangle
Overhang (m):
hub.overhang
Hub height (m):
hub.height
Hub radius (m):
hub.Rhub
Precone angle (deg):
hub.precone
Blades relative center of mass (relative to hub center) (m):
blade.cog_rel
Blade discretization nodes to average the wind speed:
blade.bladeDiscr
Generator efficiency:
gen_eff
CAD file path
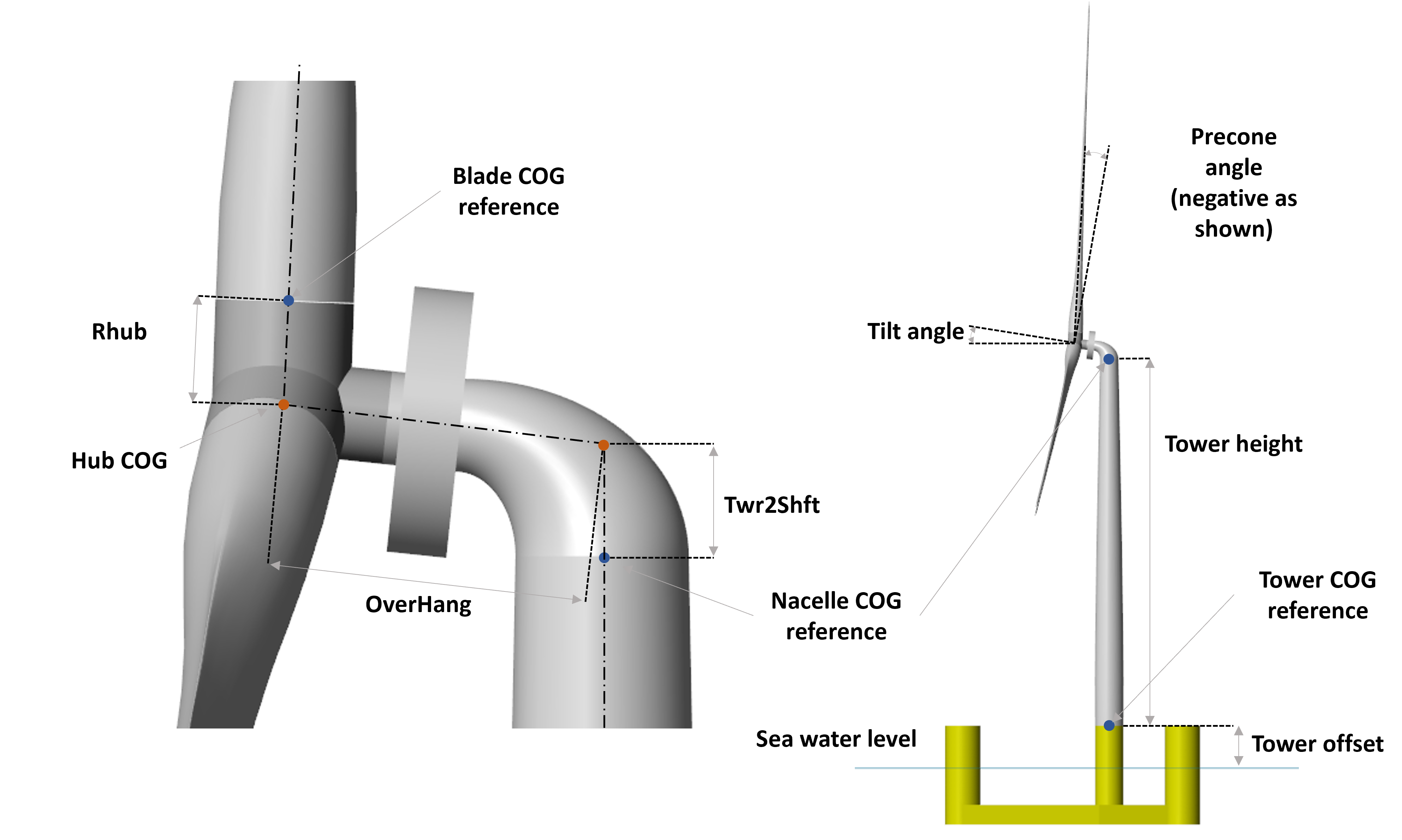
Once these dimensions are known, the positions of the centre of mass of each component in the inertial reference frame are calculated (origin at sea level and at the centre of the tower, as far as the horizontal plane is concerned), as well as the total mass and inertia.
Control Features
In MOST there is the possibility of using two different wind turbine control logics (Baseline [D3] and ROSCO [D4])
and as explained in the Theory Manual the steps to be taken in order to obtain the data needed for their simulation are the calculation
of the stationary values and the calculation of the controller gains. The first task is performed by the script Steady_States.m
in the subfolder
“Control”. Specifically, through this, the stationary values of power, rotor speed, thrust force, generator torque and collective blade pitch angle are computed
for both of the aforementioned control logics. The following variables must be specified in the script:
Value of power produced under nominal conditions and under conditions where the wind speed is greater than the nominal one:
Prated
Wind speed at which power begins to be produced (and therefore at which the generator torque becomes non-zero):
v_cutin
Wind speed above which no power is produced, and the blades rotate to a safe position (feather condition):
v_cutout
Rated first try wind speed, meaning that the actual wind speed (probably close to this) will be calculated later:
v_rated_try
Rated first try rotor speed, meaning that the actual one (probably close to this) will be calculated later:
omega_rated_try
Wind speed discretization, which indicates how many stationary values will be calculate:
v_discr
Minimum allowed value of the rotor speed (setting used only for the calculation of stationary values related to the ROSCO controller):
omega_min
Boundary wind speed value between zone 1.5 (zone with constant and equal to minimum rotor speed) and zone 2 (zone with optimal tip speed ratio), this value is used only for the ROSCO controller:
vw_R2in_try
Ratio of the maximum allowed thrust to what there would be if no limits were imposed:
max_Thrust_factor
The script calculates different stationary values according to the control logic because of their diversity. Specifically, only the ROSCO controller imposes an upper limit for the thrust force, so when the wind speed is close to the nominal one (where the force peak occurs), the blade pitch value will be slightly higher to reduce the thrust and comply with the imposed limits. The second difference is that in the Baseline controller, no minimum rotor speed is imposed, which is also the case of some turbine types for what concerns the ROSCO controller. The first step performed in the code is the calculation of the actual nominal conditions (rated wind speed, rotor speed and blade pitch angle): by means of a constrained optimisation, the values of wind speed, rotor speed and blade pitch angle are sought such that the first two are as close as possible to those set for the first attempt, with the constraint of having a thrust not exceeding the maximum and a power output equal to the rated one. In the case of the Baseline controller, the first constraint does not apply, in the case of the ROSCO controller, on the other hand, we first calculate the nominal conditions without the thrust constraint, then calculate the maximum thrust by multiplying the nominal one by the thrust factor defined in the settings and then repeat the calculation to find the correct nominal values. The optimisation relies on a function that calculates the aerodynamic forces at the hub by solving the BEM (Blade Element Momentum) theory, for more information on how this function works see ([D6] , [D7]).
The second step, performed only in the case of ROSCO, involves finding the wind speed for which transition from zone 1.5 to zone 2 (see [D4]) occurs. In both zones it is desired to maximize power, but in zone 1.5 is where there is the additional constraint of minimum rotor speed. Here, to maximize power, the rotor speed would need to be less than the minimum rotor speed, and to partially compensate for the resulting power deficit, a blade pitch angle greater than zero is used. The search for the frontier wind speed is done by an optimization that looks for the wind speed for which the difference between the rotor speed that maximizes power without imposing constraints equals the minimum wind speed. To find the rotor speed that maximizes power for a given wind speed, a second nested optimization is used.
Finally, the last step involves calculating the stationary values as the wind speed changes. It is performed by a constrained optimization through which the rotor speed and blade pitch values are sought such that the power produced is maximized while maintaining it at or below the rated power and respecting the maximum thrust limit. Once the rotor speed and blade pitch values have been found for each wind speed analysed, the steady-state values of the other quantities of interest (power, thrust, and generator torque) are evaluated.
Once the steady-state values for the two control logics have been calculated, it is possible to build the data structures needed for controller
simulation by running the Controller.m
script in the “Control” subfolder. In this script a few settings have to be defined, which can refer to
both logics or just the Baseline or ROSCO controller.
The common settings are as follows:
Maximum allowable torque rate:
torqueMaxRate
Maximum allowable blade pitch rate:
thetaMaxRate
Values needed to define the state space used to filter the rotor speed before providing this as input to the controllers:
omegaFilter
The settings only valid for ROSCO are:
Natural frequency of the electric generator torque control loop:
wn_C
Damping ratio of the electric generator torque control loop:
csi_C
Natural frequency of the blade pitch control loop:
wn_theta_ROSCO
Damping ratio of the blade pitch control loop:
csi_theta_ROSCO
Constants used in the “Set Point Smoothing” module:
kb
andkt
Gain related to the velocity (along the surge) of the nacelle, used to control floating wind turbines:
KV
Values needed to define the state space used to filter the wind speed before providing this as input to the controller:
windFilter
Values needed to define the transfer function used to filter the nacelle speed before providing this as input to the controller:
pitchFilter
Values needed to define the transfer function used as a filter in the “Set Point Smoothing” module:
SPSFilter
The settings only valid for Baseline are:
Natural frequency of the blade pitch control loop:
wn_theta_BL
Damping ratio of the blade pitch control loop:
csi_theta_BL
Regarding the Baseline controller, at the operational level, the torque law is simply computed by creating a biunivocal relationship between the steady-state (as wind speed changes) values of rotor speed and generator torque. As for the blade pitch loop, at first the value of \(K_P^\prime\) and \(K_I^\prime\) are calculated (see Baseline), after which the power to pitch sensitivity, as a function of blade pitch angle, is computed for each stationary point. To do this centered finite differences are used by calculating power via a function that solves the aerodynamics via BEM theory. Finally, we perform quadratic regression of \(\frac{dP}{d\theta_{bl}}\) so that we have, in simulation, a simple relationship between blade pitch and power-to-pitch sensitivity.
As for the ROSCO controller, however, at the operational level, in the script the \(A\) and \(B_{\theta_{bl}}\) matrices are calculated for each wind speed for which stationary values were computed through centered finite differences; regarding the \(B_{T_{gen}}\) matrix, it is calculated only once since it is constant (see ROSCO). Once the matrices are known, the values of \(K_P\) and \(K_I\) for the two controls (generator torque and blade pitch) are calculated. Finally, the minimum allowable blade pitch value is calculated using an optimization procedure; specifically, for each wind speed in region 3 (a rotor speed equal to the nominal one is assumed in this region), the blade pitch angle such that the maximum thrust occurs is found. It represents the minimum angle value that can be imposed, below which there will be a thrust greater than the maximum allowed.
Aerodynamic Loads Features
The look-up tables of aerodynamic loads are generated using the AeroLoads.m
script; the aerodynamic forces and torques are calculated as a function
of three input parameters: the wind speed, the difference between the rotor speed and the stationary rotor speed for that wind speed, and the difference
between the blade pitch angle and the steady-state angle for that wind speed. In order to calculate the required look-up tables, the user will need to
define the following variables:
Rotor speed discretization values:
o_discr
Blade pitch discretization values:
theta_discr
Discretization range of rotor speed values around steady-state one (rad/s):
o_A
Discretization range of blade pitch values around steady-state one (rad):
theta_A
The discretisation range is used to determine the aerodynamic loads near the steady states, which include all cases that are likely to be reached during operating conditions.
References
Preprint M Masciola, J Jonkman, and A Robertson. Implementation of a multisegmented, quasi-static cable model.
Neil Davis Kelley and Bonnie J Jonkman. Overview of the turbsim stochastic inflow turbulence simulator. Technical Report, National Renewable Energy Lab.(NREL), Golden, CO (United States), 2005.
Morten H. Hansen. Control design for a pitch-regulated, variable speed wind turbine. Risø National Laboratory, 2005. ISBN 8755034098.
Nikhar J Abbas, Daniel S Zalkind, Lucy Pao, and Alan Wright. A reference open-source controller for fixed and floating offshore wind turbines. Wind Energy Science, 7(1):53–73, 2022.
Evan Gaertner, Jennifer Rinker, Latha Sethuraman, Frederik Zahle, Benjamin Anderson, Garrett Barter, Nikhar Abbas, Fanzhong Meng, Pietro Bortolotti, Witold Skrzypinski, George Scott, Roland Feil, Henrik Bredmose, Katherine Dykes, Matt Shields, Christopher Allen, and Anthony Viselli. Definition of the iea wind 15-megawatt offshore reference wind turbine technical report. 2020.
S Andrew Ning. A simple solution method for the blade element momentum equations with guaranteed convergence. Wind Energy, 17(9):1327–1345, 2014.
S A Ning, G Hayman, R Damiani, and J Jonkman. Development and validation of a new blade element momentum skewed-wake model within aerodyn: preprint. 2015.
Christopher Allen, Anthony Viselli, Habib Dagher Andrew Goupee, Evan Gaertner, Nikhar Abbas, Matthew Hall, and Garrett Barter. Definition of the umaine volturnus-s reference platform developed for the iea wind 15-megawatt offshore reference wind turbine technical report. 2020.
J M Jonkman, G J Hayman, B J Jonkman, R R Damiani, and R E Murray. Aerodyn v15 user's guide and theory manual.